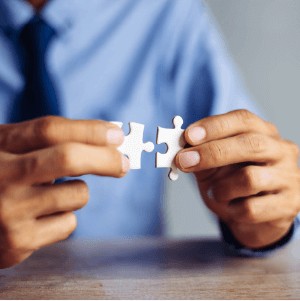
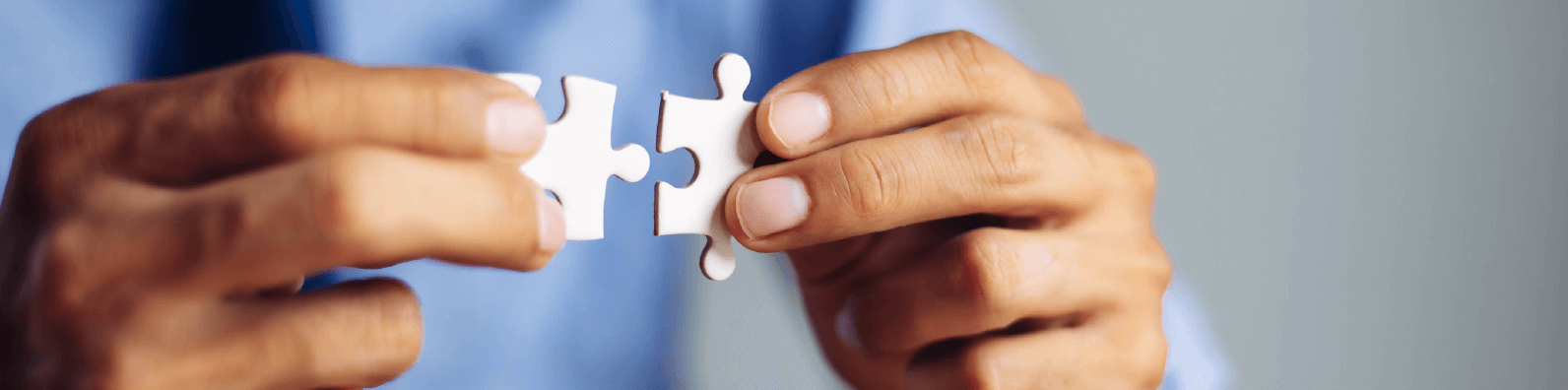
Benefits of LIMS integration with ERP and MES
Over the last few decades, computerization in the manufacturing industry was mainly focused on areas such as production planning and process control. This meant that IT development was focused on the ERP and automation layers. More recently, companies started to invest more in production execution systems like MES and LIMS solutions.
The focus of this article is to demonstrate how integrating LIMS with ERP and MES systems can help improve the overall product and production quality. The benefits mentioned in this blog are based on my hands-on experience implementing and integrating these systems.
The initial step for assigning work to the quality control lab starts in the ERP system when a production work order is created. ERP system maintains specifications of what quality tests should be performed as part of a product or production order. These specifications also dictate the valid range of test results that will determine the disposition of the product. This data can be simultaneously pushed to LIMS – to make a quality assessment, and MES – to produce the material according to the specifications.
Based on quality specifications from ERP, the Quality Control Supervisor can create standard or order specific tests in LIMS. The Supervisor can also define additional formulas for the calculation of reported results.
Most of the instruments in the quality lab can be integrated with the LIMS system. Less manual intervention means quicker processing time and fewer errors. This in turn can enable lab operators to take corrective decisions in the nick of time and help avoid unwanted problems later in the production cycle.
Integration of LIMS and MES systems ensure that test results of particular production lots are correctly associated. This allows the MES user to proceed to the next processing step if it has passed the required quality requirements.
Quality results collected by LIMS associated with disposition decisions can be automatically sent to the MES and ERP systems for further processing.
In summary, LIMS integration with ERP and MES:
Allows better utilization of staff by reducing the amount of time spent on entering data or calculating results.
Reduces data transcription errors.
Improves turnaround time.
Provides a clear picture of the WIP status of the laboratory that helps in identifying and eliminating bottlenecks.
Serves as a basis for setting up a notification framework that can enable automatic alerting for out-of-spec events.
Helps laboratories meet data management requirements set by regulatory agencies.
Allows to conduct statistical analysis on large amounts of quality data.
Gives real-time data access to other departments, such as Production Planning and Scheduling.
Facilitates ancillary record keeping of important data points that are typically kept on paper, example; calibration and maintenance records for instruments and equipment.
Streamline business processes such as quality sample storage/disposal and the COA generation and delivery.
The LIMS/ERP/MES integration has multiple benefits, and more and more companies consider this as ‘a must’ to help improve the quality and regulatory compliance for their products. There are also some drawbacks, like the additional effort required to maintain the integration and the added cost associated with that. However, the ‘drawbacks’ is something we can write about in another blog post.
Explore more of the benefits and challenges of implementing LIMS to your Lab’s productivity in this article:
About the author
Amitava Dassarma is a Senior Solution Architect at Andea with around 20 years of experience designing, leading, managing, and implementing factory solutions for companies in various manufacturing sectors. These include FMCG, Metal, Paper, Plastics, Electrical Equipment, and Automotive industries. In his previous position at IBM, he led a team of MES consultants responsible for developing and maintaining a global MES deployment for a large FMCG client. He held a similar role at Tata Consultancy Services, where he was in charge of an offshore team developing a global MES solution for a Tier 1 automotive supplier. He has hands-on experience with the DELMIA Apriso MES platform and Invensys Wonderware Factory Suite Products. Amitava received his MSc with a specialization in Mathematics from the Indian Institute of Technology, Kharagpur. Currently, Amitava, together with his family, resides in Krakow.
You also might like
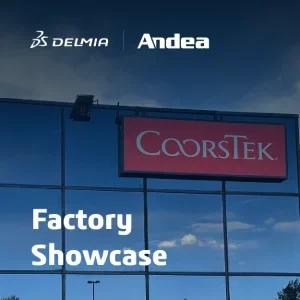
Pioneering the Path Forward: Unpacking the CoorsTek Factory Showcase
Pioneering the Path Forward: Unpacking the CoorsTek Factory Showcase The recently culminated CoorsTek Factory Showcase, in collaboration with Dassault Systèmes and hosted at CoorsTek Factory,
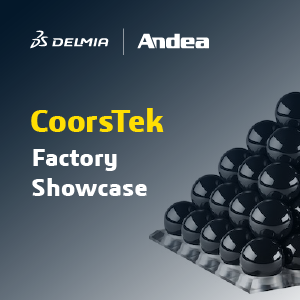
CoorsTek Factory Showcase: A Tale of Transformation in Collaboration with Andea and 3DS
CoorsTek Factory Showcase: A Tale of Transformation in Collaboration with Andea and 3DS We’re thrilled to invite you to one of the most anticipated events
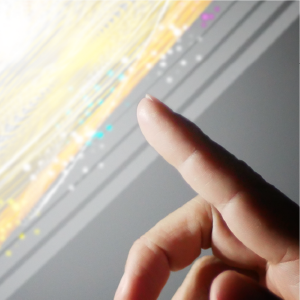
Improve your laboratory efficiency and streamlining planning processes
Improve your laboratory efficiency and streamlining planning processes Digital transformation in life science happens continuously, quickly, and in front of our eyes. Changes are driven